Comprehensive Pipeline Welding Inspection: Protecting Framework Stability
Comprehensive Pipeline Welding Inspection: Protecting Framework Stability
Blog Article
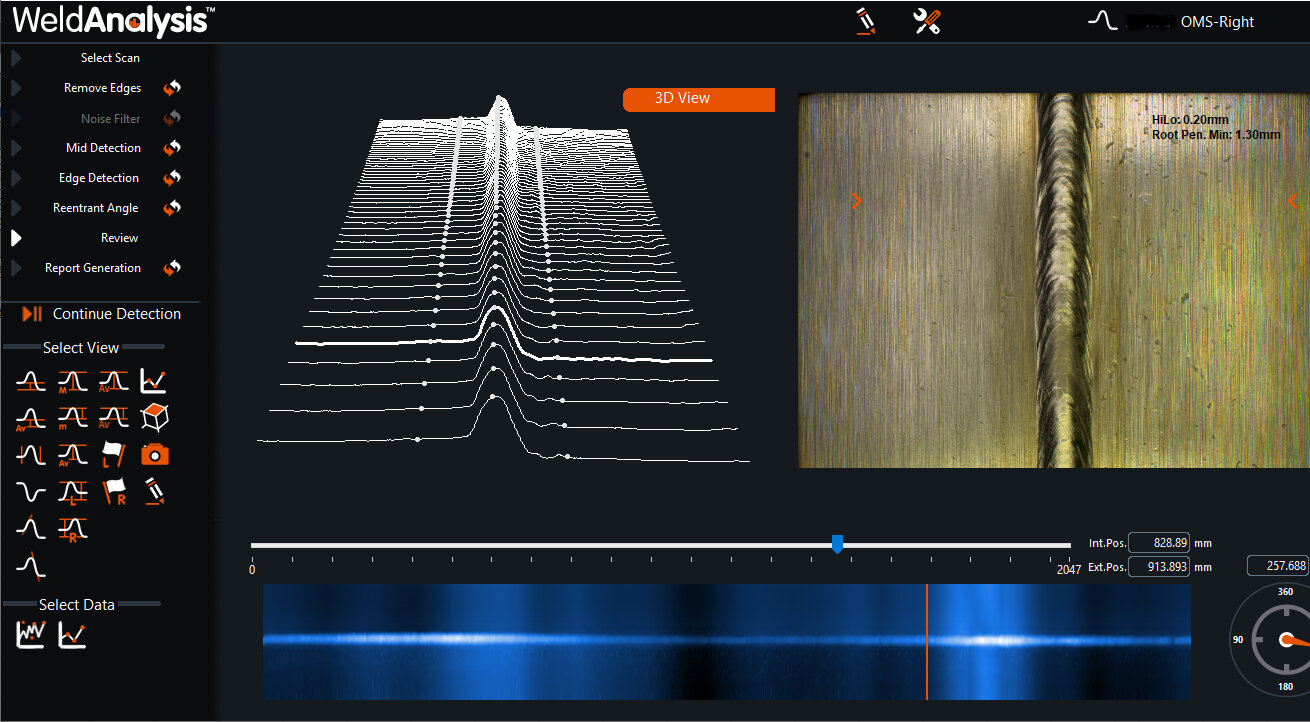
Ideal Practices for Pipe Welding Examination: Methods, Specifications, and Treatments to Accomplish Top Quality Guarantee and Conformity
Efficient pipe welding evaluation is crucial for ensuring the integrity and safety of important framework. Understanding the complexities entailed in each stage of assessment is crucial to accomplishing compliance and reliability in pipeline systems.
Value of Welding Evaluation
The integrity of welded joints is critical in guaranteeing the safety and integrity of pipe systems. Appropriate welding strategies and detailed examination processes are critical to avoid failings that can bring about disastrous events, ecological damage, and death. Pipeline Welding Inspection. Welding inspection functions as a safety net, determining flaws such as fractures, porosity, and incomplete blend before they intensify right into serious problems
Additionally, pipe systems usually run under high stress and severe conditions, making the quality of welds also extra critical. Regulative compliance is another significant aspect, as various requirements determine the quality guarantee processes that must be complied with in pipe building and construction and upkeep. Failure to conform can lead to legal implications and economic losses.

The duty of welding evaluation extends past simple confirmation of craftsmanship; it encompasses the assurance of long-term functional stability. This includes a systematic strategy that includes not just aesthetic examinations but also progressed non-destructive screening techniques. Ultimately, efficient welding examination is a financial investment in the longevity and safety of pipeline systems, ensuring they work as meant while reducing threats connected with material deficiencies.
Key Inspection Methods
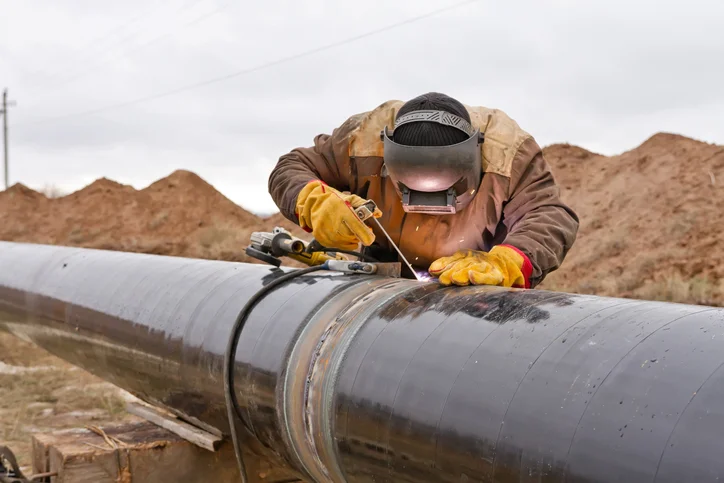
Visual evaluation, frequently the first line of protection, permits the identification of surface problems such as fractures, undercuts, and porosity. Ultrasonic screening employs high-frequency sound waves to spot internal problems, providing a thorough analysis of weld integrity. This non-destructive method is particularly reliable for identifying interruptions that might not show up externally.
Radiographic testing entails using X-rays or gamma rays to produce photos of the welded joint, disclosing internal defects. This strategy gives in-depth understandings yet may require customized equipment and security factors to consider. Lastly, magnetic fragment testing works for detecting surface area and near-surface stoppages in ferromagnetic materials, utilizing magnetic fields and fine iron particles.
Industry Standards and Regulations
Conformity with sector requirements and regulations is vital for guaranteeing the quality and safety of pipe welding examinations. These requirements provide a framework for finest methods in welding procedures, products, and evaluation strategies, allowing companies to decrease flaws and enhance the integrity of pipe systems. Key bodies such as the American Culture of Mechanical Designers (ASME), the American Welding Culture (AWS), and the International Organization for Standardization (ISO) collection forth standards that are commonly recognized and adopted within the industry.
In the United States, laws from the Pipeline and Hazardous Materials Safety Management (PHMSA) govern the safety and security of pipe operations, mandating extensive assessment methods. These requirements not just offer to shield public safety and security and the setting but also ensure compliance with contractual and lawful responsibilities. Adherence to the relevant codes, such as ASME B31.3 for procedure piping, is vital for preserving functional effectiveness and regulative compliance.
Additionally, constant updates and alterations to these requirements mirror technological improvements and evolving industry techniques, emphasizing the need for organizations to remain enlightened and train workers accordingly. Inevitably, robust conformity with established criteria cultivates trust and reliability in pipeline facilities, protecting both stakeholders and assets.
Reliable Examination Procedures
Effective assessment treatments are important for identifying potential problems in pipeline welds and making certain the total integrity of the system. A systematic technique to assessment includes numerous essential stages, including pre-weld, in-process, and post-weld examinations. Each stage plays an essential duty in preserving quality control.
Throughout pre-weld evaluation, it is vital to examine the materials and joint arrangements, ensuring conformity with job specifications. In-process inspections involve monitoring welding strategies and criteria, such as warmth input and take a trip rate, to stop problems from taking place. This phase enables real-time modifications to welding techniques.
Post-weld inspections consist of non-destructive screening (NDT) strategies like radiography, ultrasonic screening, and magnetic fragment testing. These approaches aid discover internal and surface area defects click here for more that could jeopardize the pipeline's functionality. Documents of all evaluation activities is paramount, supplying a traceable record that supports compliance with market requirements.
Training and accreditation of inspection employees further boost the effectiveness of these treatments. By sticking to an organized assessment protocol, organizations can minimize risks, make certain compliance, and eventually supply pipes that fulfill rigid safety and performance demands.
Typical Challenges and Solutions
Pipeline welding evaluation presents several usual challenges that can affect the high quality and safety and security of the end product. One considerable challenge is the variability in welding techniques and products, which can lead to irregular weld quality. To resolve this, it is important to establish standardized procedures and training for welders, making certain a consistent method across tasks.
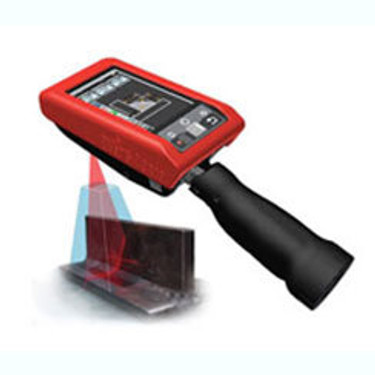
Environmental factors, consisting of temperature level and moisture, can additionally impact the welding procedure, potentially resulting in cracks or insufficient blend. Applying regulated settings and adhering to pre-weld treatments can reduce these dangers.
Verdict
Finally, the implementation of best practices for pipeline welding inspection is essential for making sure quality control and conformity with market criteria. An extensive method, integrating different strategies such as aesthetic, ultrasonic, and radiographic testing, facilitates the identification of flaws throughout all phases of the welding process. Pipeline Welding Inspection. Adherence to developed policies and reliable examination blog here procedures not just improves the integrity and safety of pipe systems but also minimizes threats related to welding issues, consequently promoting general functional stability
Compliance with market criteria and policies is important for guaranteeing the high quality and safety and security of pipeline welding inspections. These standards give a structure for ideal practices in welding procedures, products, and examination strategies, allowing organizations to lessen defects and improve the integrity of pipe systems.In the United States, laws from the Pipe and Hazardous Products Security Management (PHMSA) govern the safety read the full info here and security of pipe procedures, mandating extensive evaluation protocols. A methodical method to inspection incorporates a number of essential stages, including pre-weld, in-process, and post-weld inspections.In verdict, the implementation of finest methods for pipe welding inspection is necessary for making certain high quality assurance and compliance with sector criteria.
Report this page